Subsection 6.2.4 Air Intake System
Because diesel engines requires close tolerances to achieve the required compression ratio, the air entering the engine must be clean, free of debris, and as cool as possible. The air intake system is designed to perform these tasks. Air intake systems vary greatly from vendor to vendor but are usually one of two types, wet or dry.
In a wet filter intake system, as shown in Figure 6.2.4, the air is sucked or bubbled through a housing that holds a bath of oil such that the dirt in the air is removed by the oil in the filter. The air then flows through a screen-type material to ensure any entrained oil is removed from the air.
In a dry filter intake system, paper, cloth, or a metal screen material is used to catch and trap dirt before it enters the engine, similar to the filters used in automobile engines.
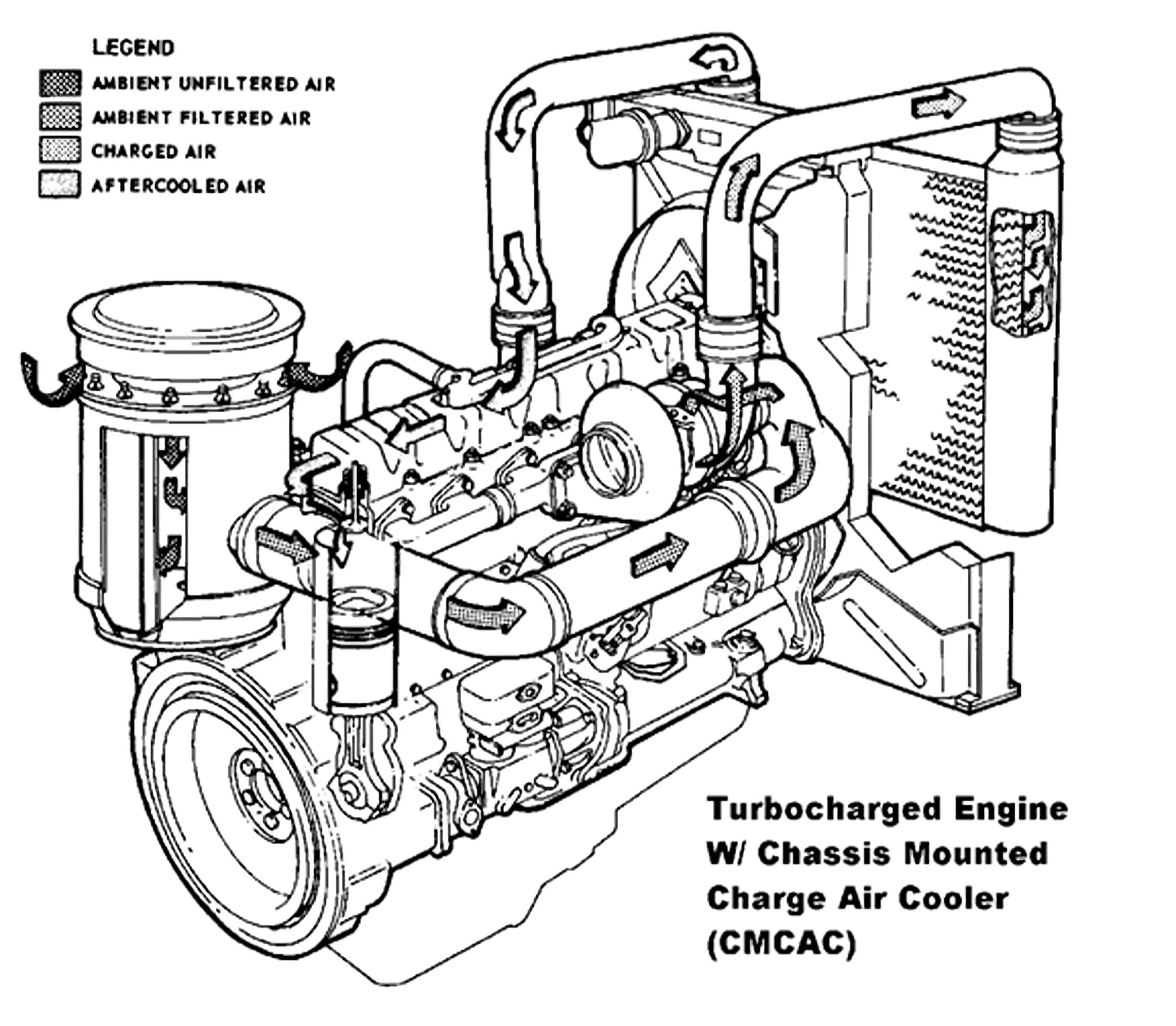
In addition to cleaning the air, the intake system is usually designed to take fresh air from as far away from the engine as practical, usually outside of the engine’s building or enclosure. This provides the engine with a supply of air that has not been heated by the engine’s waste heat. The reason for ensuring that an engine’s air supply is as cool as possible is that cool air is more dense than hot air. This means that, per unit volume, cool air has more oxygen than hot air. Thus, cool air provides more oxygen per cylinder charge than less dense, hot air. More oxygen means a more efficient fuel burn and more power. After being filtered, the air is routed by the intake system into the engine’s intake manifold or air box.
The manifold or air box is the component that directs the fresh air to each of the engine’s intake valves or ports. If the engine is turbocharged or supercharged, the fresh air will be compressed and possibly cooled before entering the intake manifold or air box. The intake system also serves to reduce the air flow noise.
Turbocharging and supercharging are two methods used to increase the power output of a diesel engine by forcing more air into the combustion chamber.
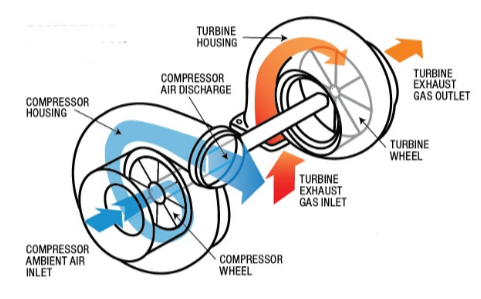
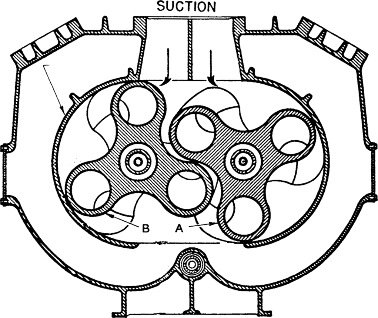
Turbocharging.
Turbocharging occurs when the engine’s own exhaust gases are forced through a turbine (impeller), which rotates and is connected to a second impeller located in the fresh air intake system. The impeller in the fresh air intake system compresses the fresh air.
The compressed air serves two functions. First, it increases the engine’s available power by increasing the maximum amount of air (oxygen) that is forced into each cylinder. This allows more fuel to be injected and more power to be produced by the engine. The second function is to increase intake pressure. This improves the scavenging of the exhaust gases out of the cylinder. Turbocharging is commonly found on high power four-stroke engines. It can also be used on two-stroke engines where the increase in intake pressure generated by the turbocharger is required to force the fresh air charge into the cylinder and help force the exhaust gases out of the cylinder to enable the engine to run.
Supercharging.
Supercharging an engine performs the same function as turbocharging an engine. The difference is the source of power used to drive the device that compresses the incoming fresh air. In a supercharged engine, the air is commonly compressed in a device called a blower. The blower is driven through gears directly from the engines crankshaft. The most common type of blower uses two rotating rotors to compress the air. Supercharging is more commonly found on two-stroke engines where the higher pressures that a supercharger is capable of generating are needed.
Supercharging provides an immediate power boost without the lag often associated with turbochargers, although supercharging is generally less efficient because it draws power directly from the engine.