Subsection 5.2.2 Gate Valves
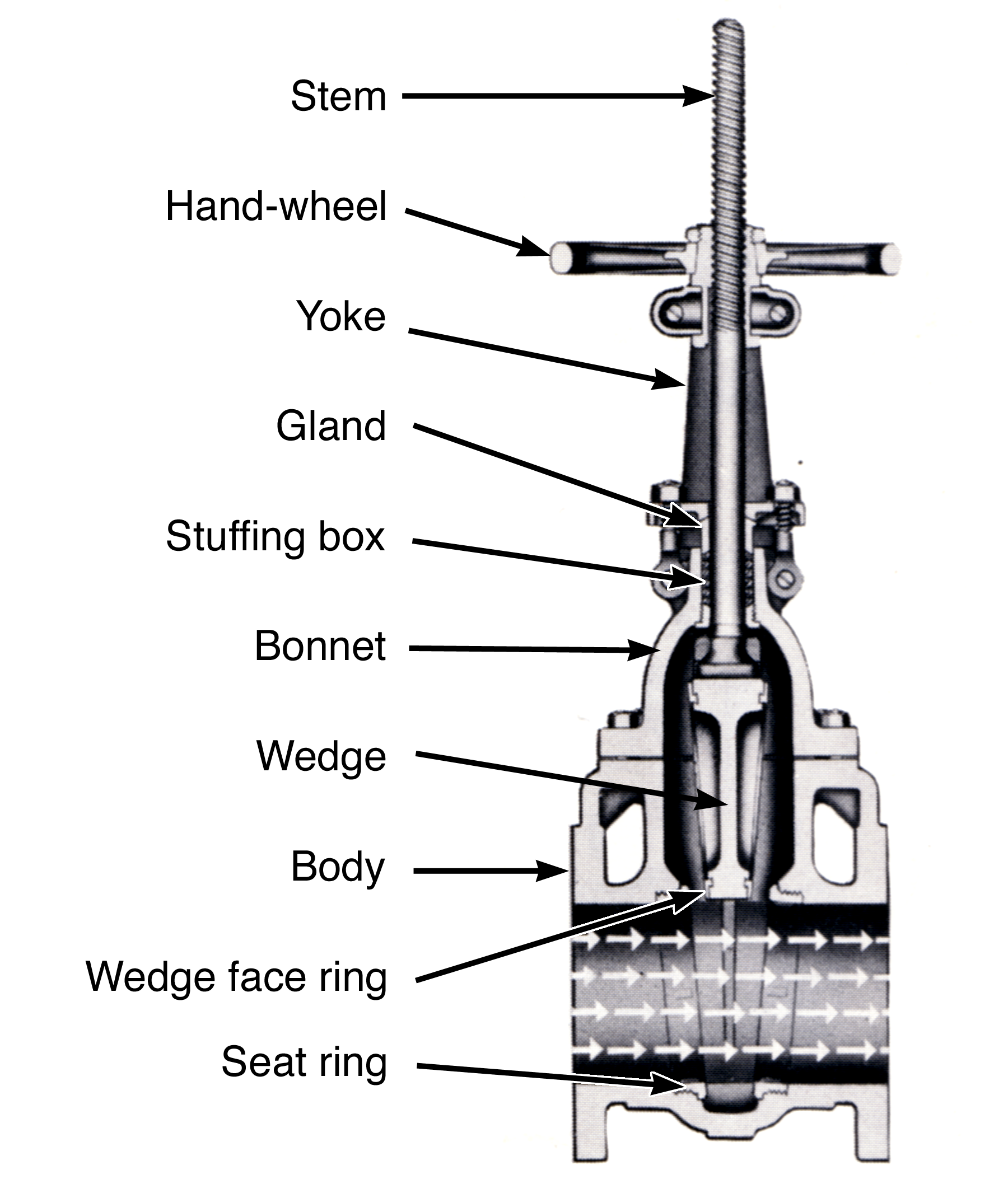
A gate valve, Figure 5.2.5, is called for when you don’t need to regulate flow, only turn it on or off. To open a gate valve, the moving part, called the gate or wedge, is moved across to the fluid flow path unblocking the opening in the valve, called the seat. The gate is actually slid off the surface of the seat sideways. Sliding the gate back over the seat blocks fluid flow and closes the valve.
When open, fluids follow a straight, unobstructed path through the valve creating a minimal pressure drop across the valve. This is the principle advantage of a gate valve over a globe valve; it has a much lower restriction to flow when fully open.
Gate valves are designed to be fully open or fully closed. They should not be left partially open to regulate fluid flow. The fluid flow under a partially open gate causes the gate to swing back and forth. This could cause the gate to hit the seats (sometimes called chattering) creating damage to the machined surfaces of the seat and gate leading to leakage when the valve is closed.
A gate valve, like a globe valve, is constructed in two basic parts, the body, and the bonnet.
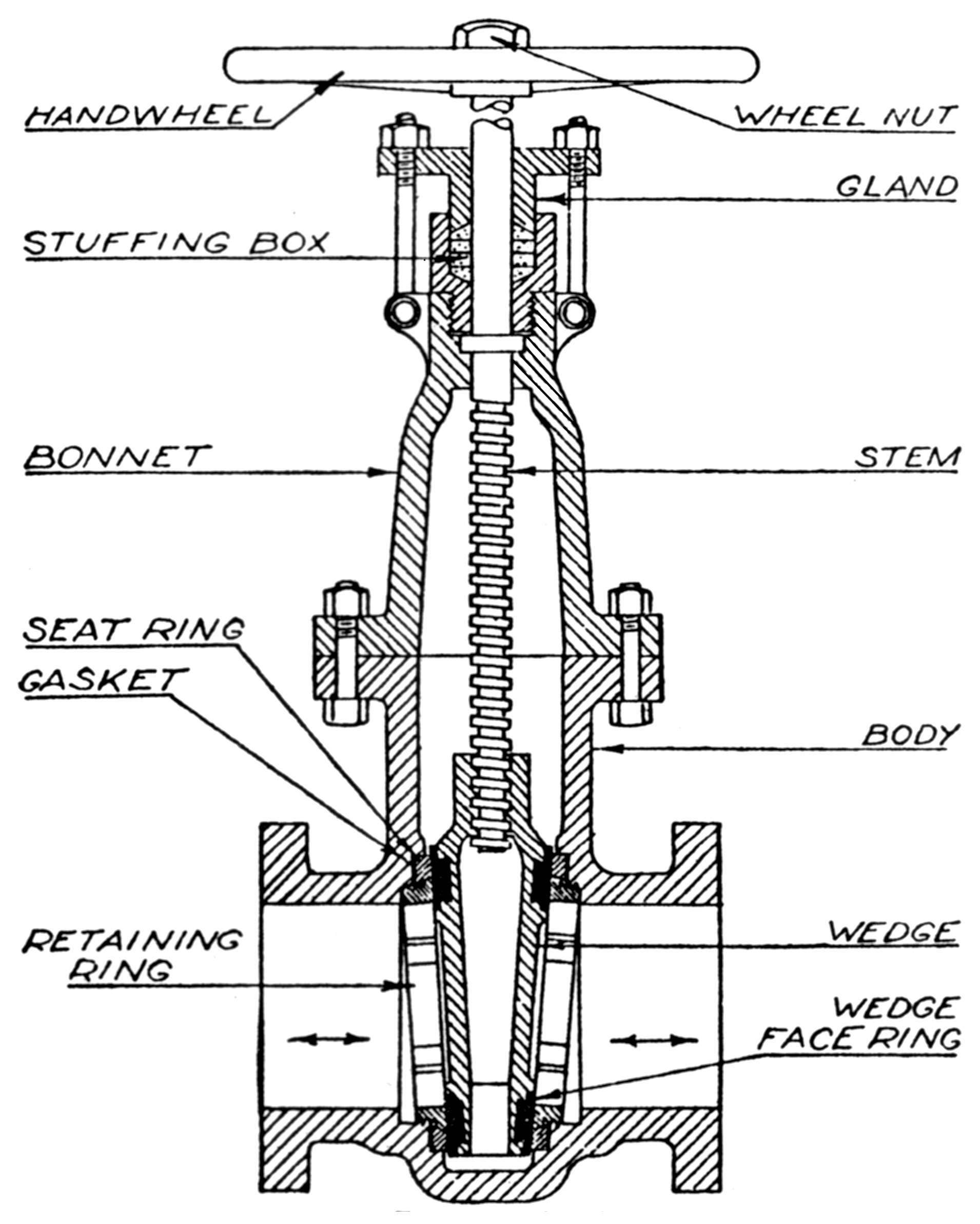
Body.
Piping inlet and outlet connections are fitted to the body 180° apart only, similar to the straight globe valve. Piping connections to the body are the same as a globe valve: threaded, flanged, etc.
The body has two seats inside facing each other. One surrounds the inlet opening and the other the outlet opening. The distance between the seats nearest the bonnet opening is greater than the distance between the seats at the bottom of the valve body creating a wedge shape between them. The gate is moved down from the bonnet location between the two seats. It has a machined surface on both sides and has a wedge shape that matches the two seats forcing it to seal tightly against both seats when it is pushed down between them.
The upper part of the body and sometimes the lower part of the bonnet form a large cavity for the gate to retract into as the valve is opened. Since the gate slides off the seats sideways, it must be moved more than the full diameter of the seat opening to be fully open. This is why most gate valves are taller than globe valves of a comparable size.
Bonnet.
The bonnet houses the equipment necessary to operate the gate and is attached and sealed to the body using the same methods as on globe valves.
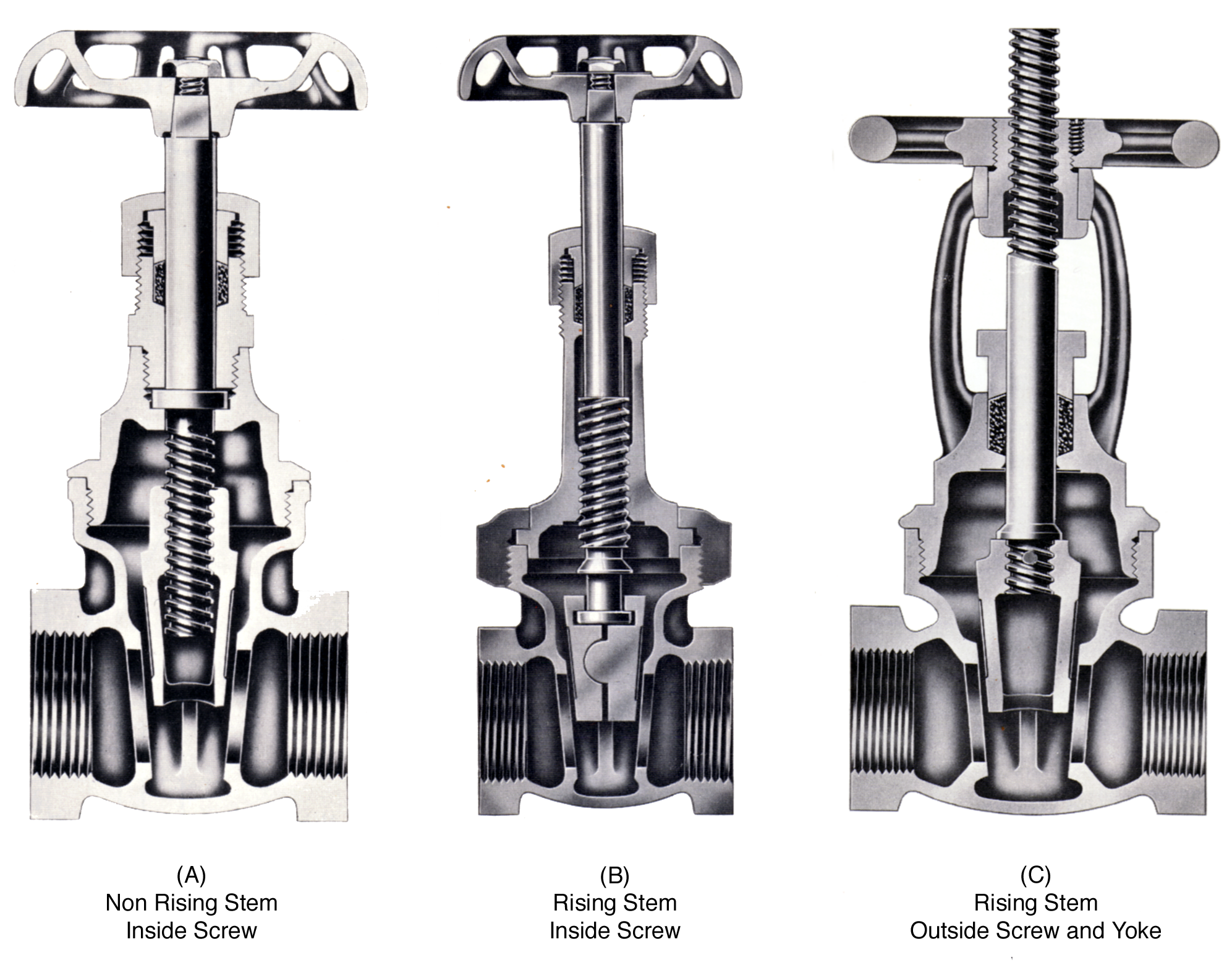
Gate valves are available in different types of stem connections. Figure 5.2.7 illustrates three different types.
- Non-rising stem, inside screw (A) The stem screws down into the valve gate as the valve is opened. In this type the stem does not rise or fall outside the valve body as the valve is opened or closed, it simply rotates.
- Rising stem, inside screw (B) The stem rises outside the valve as the valve is opened, but the stem screw operates inside the body of the valve. When operated, the valve stem in this design rises and rotates.
-
Rising stem, outside screw and yoke (C) The stem screw operates at the level of the hand-wheel, so the stem rises independently of the hand-wheel as the valve is opened. The valve stem rises, but does not rotate. Instead of the valve stem rotating, the hand-wheel rotates the yoke bushing pulling the stem straight up. Valve stem threads can be easily cleaned and lubricated in this design.Outside screw and yoke design is required on gate valves when diameters exceed 3" and pressures exceed 600 psig.
Notice that in both type A and B, the stem threads are exposed to the fluids flowing through the valve. Fluids can eventually corrode the threads and fluids with solids entrained can cause the threads to bind up and create excessive wear.
Valves with rising stems are used when it is important to know by immediate inspection whether the valve is opened or closed. The outside screw and yoke type easily indicates valve position due to the stem extending out beyond the center of the valve wheel when it is open.
The non-rising type is the least likely to leak in the packing area and requires less installation space.