Subsubsection Reciprocating Pumps
In reciprocating pumps, a power source drives a piston or plunger back and forth in a cylinder. This action pushes liquid out into the discharge on the discharge stroke, and draws liquid into the cylinder, from the source of supply, on the suction stroke. For each stroke, the same quantity of liquid enters and leaves the cylinder. The fluid flow through the pump is controlled by two check valves, one in the suction line and the other in the discharge line of the pump.
Figure 5.3.7 shows a steam driven reciprocating pump. The steam piston (7) is driven up and down by steam, delivering power to the liquid piston, or (69), which pumps the liquid. When the liquid piston (69) is moved down, the area above the piston is on a suction stroke. As the piston moves down in cylinder (72), the increase in cylinder volume causes a decrease in cylinder pressure. When the pressure in the cylinder drops below atmospheric pressure (creating a vacuum in the cylinder), the atmospheric pressure on the liquid in the suction tank forces the liquid up the suction pipe, through suction valve (85) and into the cylinder. Atmospheric pressure plus the liquid pressure in the discharge pipe create a pressure higher than the pressure in the cylinder. This holds the discharge valve (84) closed. When the piston begins to move up on the discharge stroke, a decrease in cylinder volume occurs, attempting to compress the liquid. This results in an increase in liquid pressure in the cylinder. As soon as the cylinder pressure exceeds the pressure in the suction pipe, the suction valve (85) is forced closed. As the piston continues to move up, the liquid pressure in the cylinder continues to rise. When the liquid pressure in the cylinder exceeds the pressure in the discharge pipe, the discharge valve (84) opens and fluid flows from the cylinder into the discharge line. This process repeated many times can build up a considerable discharge head (pressure) on the discharge side of the pump.
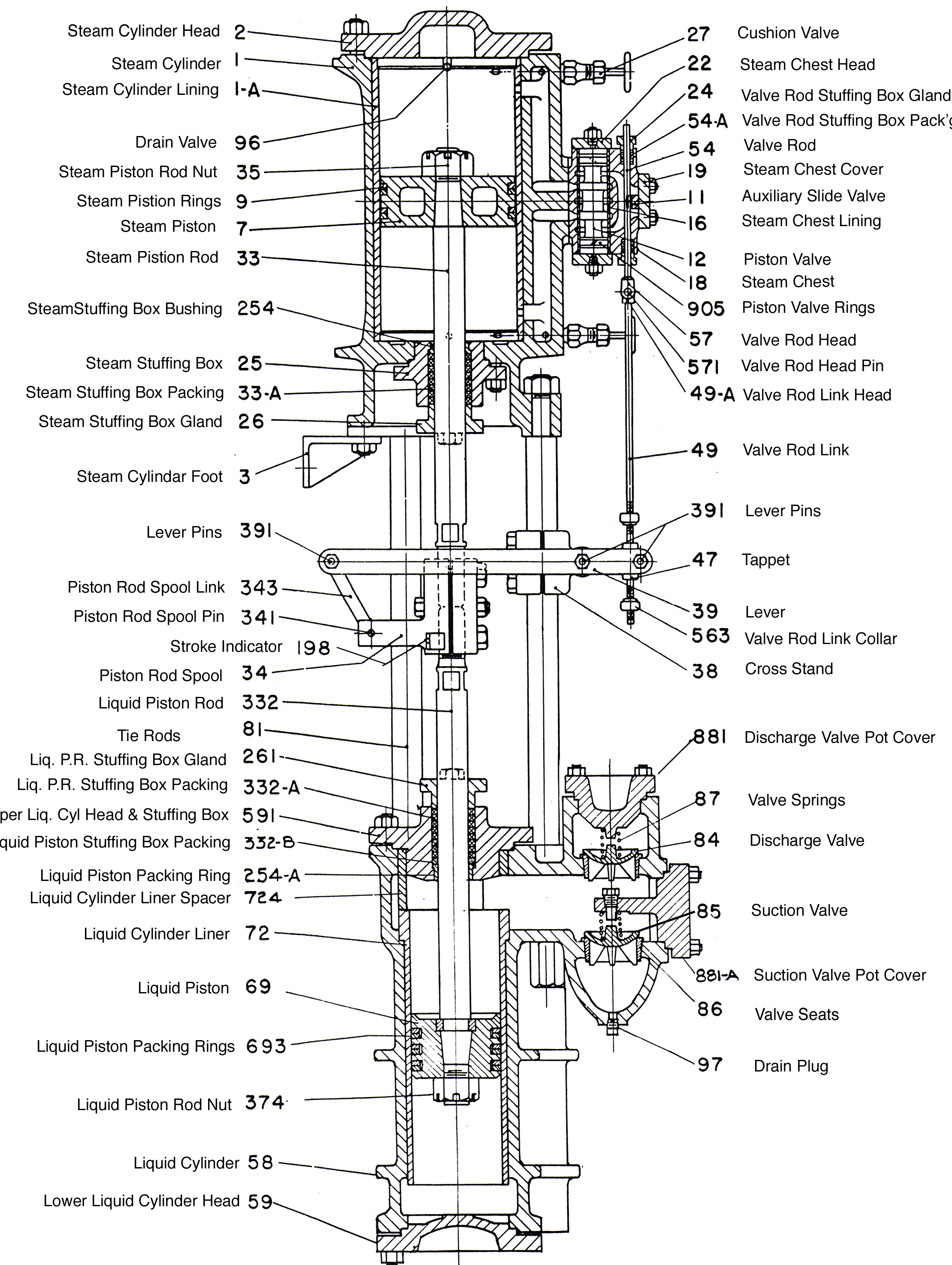
Reciprocating pumps are classified as positive displacement, self-priming and most are constant delivery, except for some specialized hydraulic pumps. Reciprocating pumps are additionally classified by the characteristics in List 5.3.8
- Bore
- The bore is the inside diameter (ID) of the cylinder, usually measured in inches.
- Stroke
- The stroke of a pump is the maximum distance the piston can travel from one end of the cylinder to the other, usually measured in inches.
- Single stroke
- The motion of the piston from one extreme to the other.
- Double stroke
- The motion of the piston from one end of the cylinder to the other and back to its original starting point. It is equal in distance to two single strokes. It is also a complete operating cycle for that piston (piston has returned to its original starting point and now the cycle repeats.)
- Single-acting
- A single acting pump uses only one side of the piston to pump liquid. It is normally the side not attached to the piston rod or the connecting rod.
- Double-acting
- A double acting pump is fitted with suction and discharge valves on both sides of the piston, allowing the piston to pump liquid on both strokes of the pump cycle.
- Direct-acting
- The engine used is a steam reciprocating engine. The steam piston is pushed back and forth in the steam cylinder and the rod attached to the steam piston extends into the liquid cylinder and is directly attached to the liquid piston in the reciprocating pump. The engine produces the mechanical motion the reciprocating pistons require, hence; direct-acting.
- Indirect-acting
- The power sources provide rotary motion to this type of reciprocating pump. The rotary motion of the power supply source must be converted to reciprocating motion at the pistons using a mechanical device called a crankshaft.
- Simplex
- Only one liquid cylinder and piston are built into the pump. They may be operated by a steam reciprocating engine or more commonly today from a rotary engine via a crankshaft and connecting rod.
- Duplex
- Two liquid cylinders and pistons are built into a common pump housing. Each cylinder may be operated by its own separate reciprocating engine. (with both engines built into the common housing) More commonly today, they are driven from a rotary engine via a crankshaft and connecting rods.
- Triplex
- Three liquid cylinders and pistons are built into a common pump housing. Normally driven by a rotary engine via a crankshaft and connecting rods. Although direct-acting and indirecting-acting pumps can be built with more than three cylinders, they are not very common.